
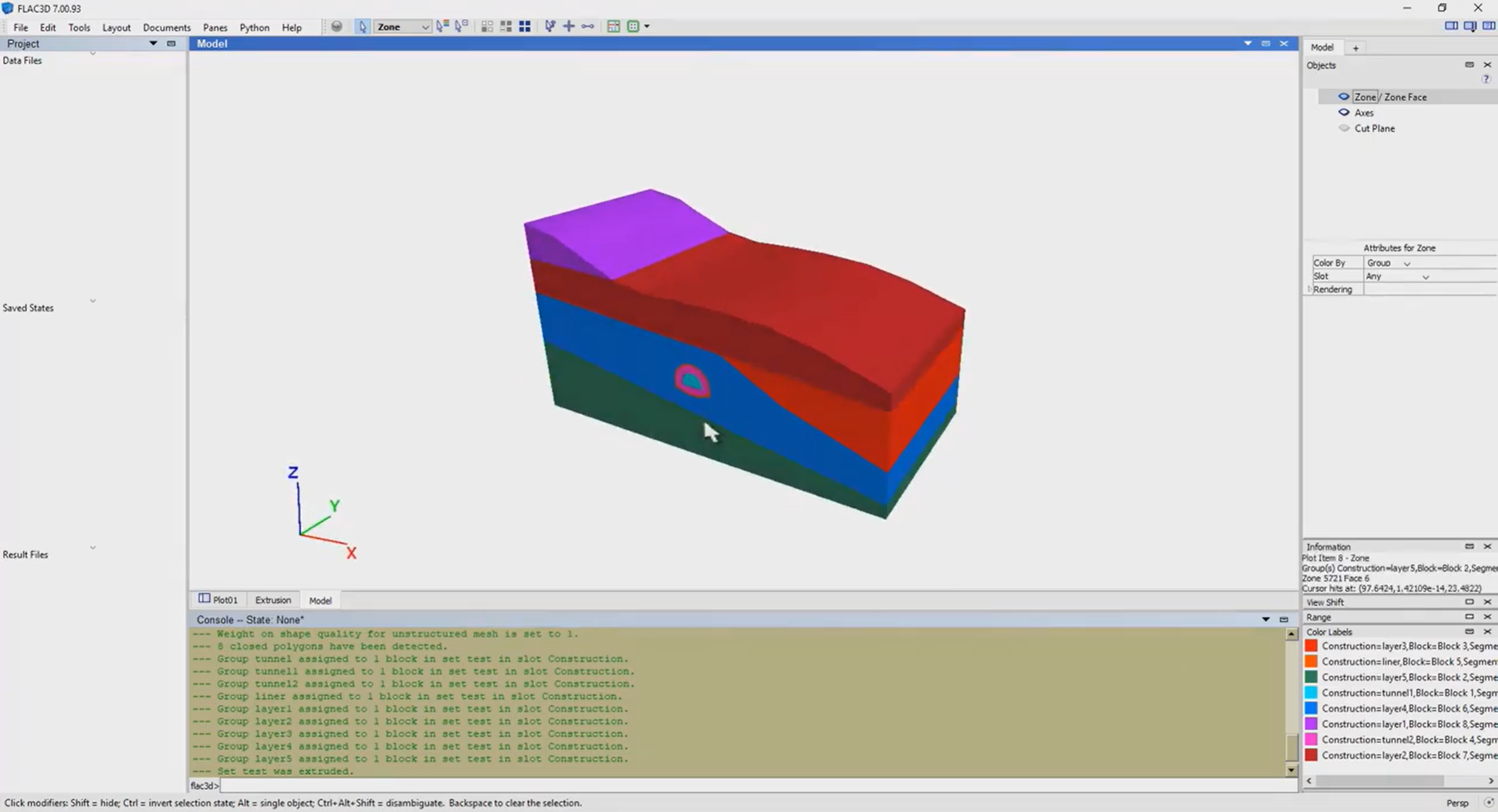
Monitoring like acoustic emissions will be measured during the test execution. High compressive stresses in addition to some tensile stresses might induce some AE (acoustic emission) activity in the upper part of the hole from the very beginning of the test and are thus potential areas where AE activities may be detected. This makes the damaged area in some degree smaller. When the other hole is pressurized with a 0.8 MPa confining pressure it yields that 5 MPa more stress is needed to damage the rock than without confining pressure. These could be considered the areas where damage may occur during the in-situ test. Has exceeded were identified and they extended to about two meters down the hole wall. The results from FLAC3D model showed that only regions where the crack initiation stress The rising temperature due to thermal expansion induces stresses in the pillar area and after 120 days heating the stresses have increased about 33% from the excavation induced maximum stress of 150 MPa to 200 MPa in the end of the heating period. According to the modeling the initial temperature rises from 15 deg C to about 65 deg C in the pillar area during the heating period of 120 days. FLAC and PFC were coupled to minimize the computer resources and the computing time.
THE TEST SITE WILL BE MODELED IN FLAC3D CODE
Cracking and damage formation were modeled in the area of interest (pillar between two large scale holes) in two dimensions by using the Particle Flow Code (PFC), which is based on particle mechanics.
THE TEST SITE WILL BE MODELED IN FLAC3D SOFTWARE
The elastic thermo-mechanical modeling was carried out in three dimensions because of the complex test geometry and in-situ stress tensor by using a finite-difference modeling software FLAC3D. The study is focused on understanding and control of progressive rock failure in hard crystalline rock and damage caused by high stresses. SKB is planning to perform a large-scale pillar stability experiment called APSE (Aespoe Pillar Stability Experiment) at Aespoe HRL.
